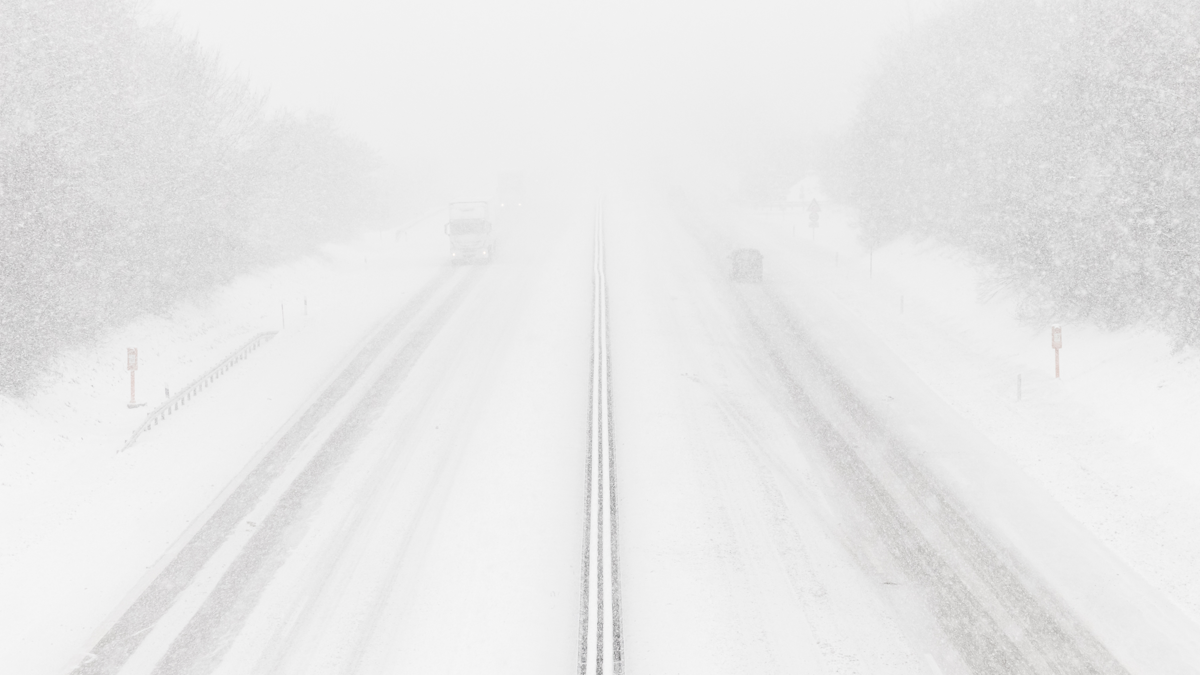
First it was COVID-19, and more recently it has been the significant weather-related events that have caused significant disruption to global logistics and the supply chain. It seems to me that there are lot more things disrupting the movement of goods, whether from a pandemic, natural disaster, or significant technological developments.
While you can’t plan for what the specific disruption will be, you can almost be guaranteed that at some point your business will face an unforeseen challenge. The question is: How prepared are you? If you do not have a disaster plan or have not updated yours in a while, now is probably a good time to do so.
I am not particularly fond of the words “disaster plan” and prefer to think of it as preparedness planning or business continuity planning. It’s about what you need to do to ensure your business can continue operating or adapt if faced with something that significantly disrupts the environment where you operate.
The first step in the process is to assess your risks. Not all businesses are subjected to risks from the same things. Common things to consider include natural hazards such as tornadoes, floods, hurricanes, forest fires, and earthquakes. Also consider health hazards like the coronavirus and unexpected disruptions such as workplace violence, power outages, etc.
Unfortunately, too often we get complacent about the hazards that can happen, especially environmental hazards, and begin to think that things won’t be as bad as predicted. I contend it is better to be over prepared and not need to implement your plan than to be without a plan when you need it.
The first element of the plan should focus on your people and ensuring their safety. Develop a check-in system that will be deployed in the event of a disaster so you can account for the whereabouts of everyone who works for you. In addition, assign responsibility for executing various parts of the plan to key people in the organization. This will ensure the plan gets carried out properly.
Next you need to focus on your assets. If your vehicles are damaged or destroyed, what arrangements have you made to get short-term replacement vehicles so you can continue operating until you can permanently replace the lost assets and repair the damaged ones?
Also, what happens if the buildings you operate out of are damaged or destroyed? Your business continuity plan should include options for moving your operations to a temporary location for as long as needed. If you operate out of multiple locations, it could be as simple as shifting everything to an unaffected site. But you need to have a plan in advance for what that would look like and how it would take place.
And what about supply chain disruption? What if one of your suppliers has to shut down production for a period of time? Will you be able to get replacement products from another supplier? Don’t wait until a significant disruption occurs to try to establish alternate sources of supply.
To be truly effective, your business continuity plan must look at every aspect of your operation and determine what changes need to be made in order to allow each area of your business to continue to operate following a significant disruption — no matter what that disruption is.
The bottom line is you can’t wait for a disaster or significant disruption to occur to figure out how you will respond to it. The time to plan is well before you are faced with a problem. Failure to do that could lead you having to close your business forever. And that would be a real disaster.
Patrick Gaskins, senior vice president of Corcentric Fleet Solutions, oversees both sales and operations for Corcentric’s fleet offerings. Over the past 10 years, Gaskins has grown the fleet services area of Corcentric’s business by implementing a best-in-class asset management database and a data-driven approach to providing Corcentric clients with visibility into all areas of their fleet spend. He joined Corcentric in 2010, bringing over 30 years of experience as a financial services professional in the transportation industry. Gaskins leads a team of industry experts who work with a supply base of over 160 manufacturers to help the country’s largest fleets manage all aspects of their fleet operations and fleet related spend. Gakins earned his BBA in Finance from the University of Miami, FL, and his CTP certification from the National Private Truck Council.
The other day on the local news, I saw that Fort Wayne, Ind., utility trucks were jumping on the freeway heading to Kentucky and Tennessee to lend support to utilities in those states that were anticipating power lines being down because of an impending ice storm. Earlier in that same week, someone had mentioned that they thought utility trucks were perfect for electrification because they are owned by the utilities and usually don’t travel very far.
The key here is “usually” and that got me thinking about the importance of fully understanding duty cycle is not just looking at average trips or average days when making decisions on how to spec a vehicle.
On the surface it seems to make good sense to electrify all utility trucks because they don’t accumulate a lot of miles and they return to base, so charging is simplified. But the reality is that in times of emergency, utility trucks are sent far beyond their normal area of operation. If all the utility trucks were electric powered that sharing might not be able to happen. They couldn’t make the long-distance trip and unless the needed charging infrastructure was in place, couldn’t charge once they got there.
Does that mean that utilities should not begin moving to electrification? The answer is obviously, no. For most utility trucks, it is often business as usual and that means switching to battery-electric vehicles make a great deal of sense. However, if they are part of a bigger emergency response effort that requires trucks to move about the country as needed in response to emergency needs, then at this point going all electric is not an option.
Utilities — like most fleets — can’t afford to have extra equipment sitting around that does not get used, so it can be tricky to figure out just how many trucks in the fleet can be electric. The only way to make that decision is to do an in-depth analysis of how often a truck needs to be deployed in an emergency situation and then use that information to make sure there are the right mix of trucks in the fleet.
You can’t spec for the average or the usual. No matter what kind of fleet you are, you need to dive into the details of your operation to find the right mix of not only vehicles but powertrains that are going to allow you to operate both efficiently and profitably, all the while keeping in mind that we are moving to zero-emissions future in which electric vehicles will dominate.
I am not certain what the best solution to this is, but I do know that using “usuals or averages” solely won’t work. As a friend tells me often, there is no average truck, route or payload.
"how" - Google News
February 25, 2021 at 09:54PM
https://ift.tt/37I0Yuz
How to plan ahead for the next disaster - Fleet Owner
"how" - Google News
https://ift.tt/2MfXd3I
https://ift.tt/3d8uZUG
Bagikan Berita Ini
0 Response to "How to plan ahead for the next disaster - Fleet Owner"
Post a Comment